ZCC Tungsten Carbide Milling Inserts SEKR1203 Cutter For Milling Factory Wholesale
Basic Information
1.Tungsten carbide tools for Turning inserts
CNMG/TNMG/WNMG/DNMG/SNMG/VNMG/CCMT/DCMT/SCMT/TCMT/VBMT/KNUX
2.Tungsten carbide tools for milling inserts
APKT/APMT/RPKW/RDKW/RCMT/SPKN/TPKN
3.Tungsten carbide tools for Aluminium inserts cutting
CCGT/DCGX/SCGX/TCGX/VCGX
4.PCD &PCBN Tungsten carbide tools turning for inserts
CNGA/DNGA/SNGA/TNGA/VNGA/CCGW/DCGW/TCGW/VBGW
Application
Main Application: For processing carbon steel, cast iron, stainless steel
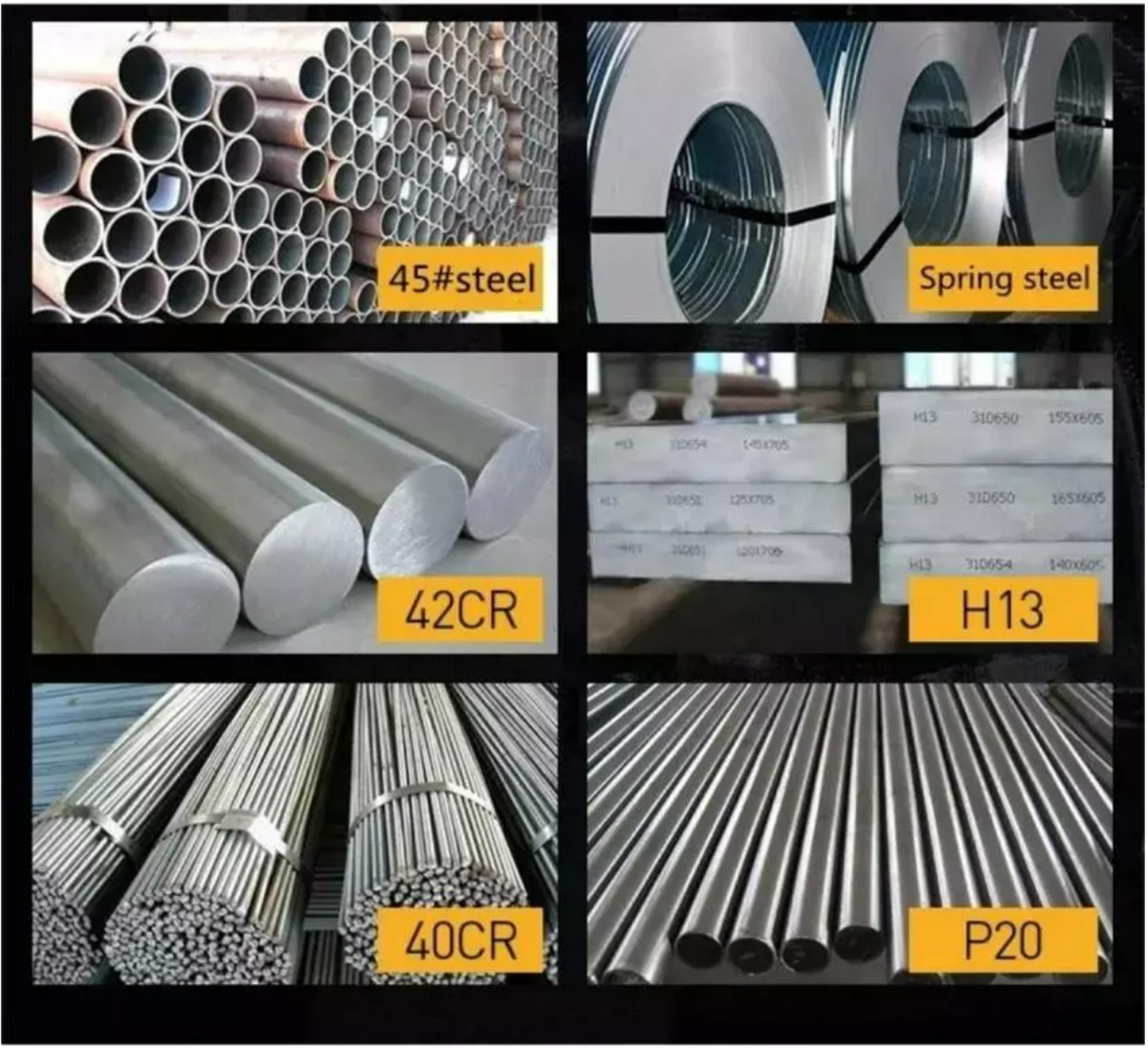
Industry of application:
CNC turning and milling tungsten carbide tools products inserts are widely used in: Automotive manufacturing industry, Mold manufacturing industry, Aviation industry, Defense industry, Heavy processing industry and many other field.
we can produce various types tungsten carbide cutting tools insert according to different customized drawings.
we can provide the overall supporting solutions for the machining field.
Material Grade Introduction
Introduction of turning material introduction:
7215 has high strength and toughness of high toxicity resistance matrix, combined with MT-TICN, AL2O3,TIN excellent combination of coating process, and then through advanced coating post-treatment to eliminate the internal stress of blade layer, suitable for ordinary steel finishing.
7125 edge safety of high strength, high toughness matrix combined with MT-TICN and superfriction AL203 coating process, and then through advanced coating post-treatment process to eliminate the internal stress of the coating, suitable for ordinary steel rough processing, semi-finishing and part of the workpiece roughness requirements are not high finishing.
4025 high corrosion resistance, and through a certain pressure sintering process of high strength matrix and MT-TICN and super thick AL2O3 coating excellent combination, with advanced coating post-treatment technology to obtain smooth coating surface, suitable for the rough machining, semi-finishing and finishing of cast iron.
1030 fine grain, excellent deformation resistance and through the pressure sintering process to obtain ultra-high strength and wear resistance matrix, with nano PVD coating process, and then through advanced coating post-treatment to obtain smooth coating surface, suitable for ordinary steel finishing, quenched steel, chromium plated steel and stainless steel semi-finishing and finishing.
1120 ultra-fine grain, excellent deformation resistance, and through the pressure sintering process to obtain high strength and wear resistance matrix, with nano SI containing PVD coating process, after advanced coating post-treatment to obtain smooth coating surface. Suitable for grooving and cutting of ordinary steel, hardened steel and cast iron.
Introduction of milling and drilling materials
1030 NC-TIALN coating combined with strong and ductile matrix of fine particles is suitable for coarse and semi-finished milling of all kinds of processed materials. Grooving, cutting and drilling of half aperture.
1130 NC-TIALN coating containing SI is combined with fine particles and good toughness of hard alloy matrix, suitable for stainless steel, cast iron phase and semi-finish to processing, to achieve a perfect combination of safety and wear resistance.
5035 added wear and high temperature resistance elements of CVD coating, high coating hardness and excellent high temperature resistance to provide effective protection for the cutting edge, special coating treatment technology, coating and matrix more firmly, suitable for high temperature alloy, titanium alloy materials precision milling processing.
5135 NC-TIALN coating containing SI combined with carbide matrix with excellent impact toughness, suitable for steel parts, stainless steel, grooving, cutting deep cutting, fast feeding processing and large aperture drilling processing.
Product Specifications
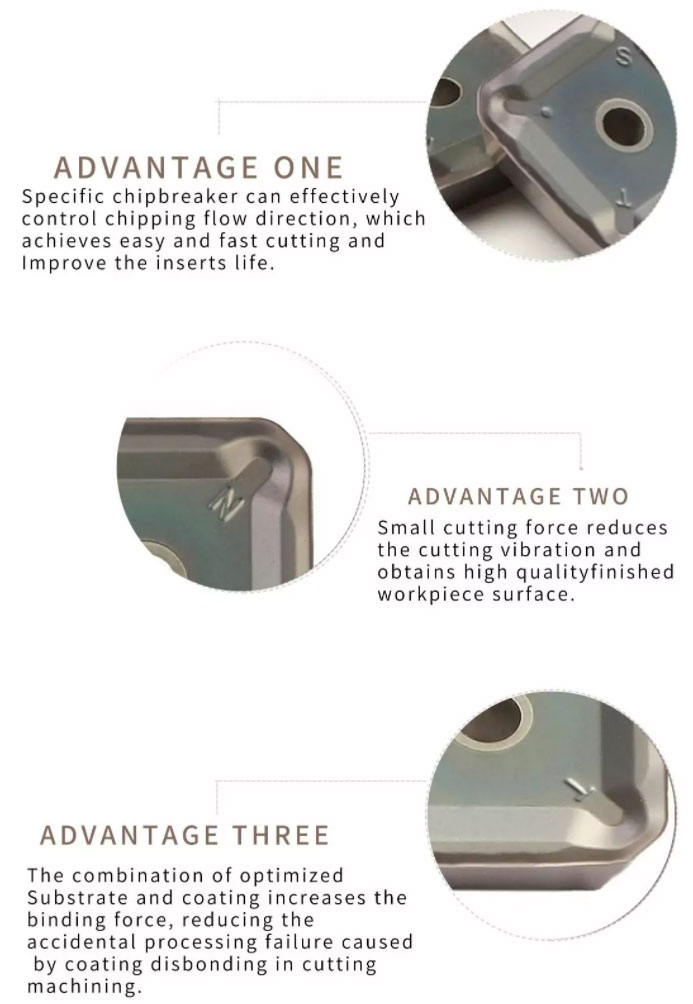
Coating Display
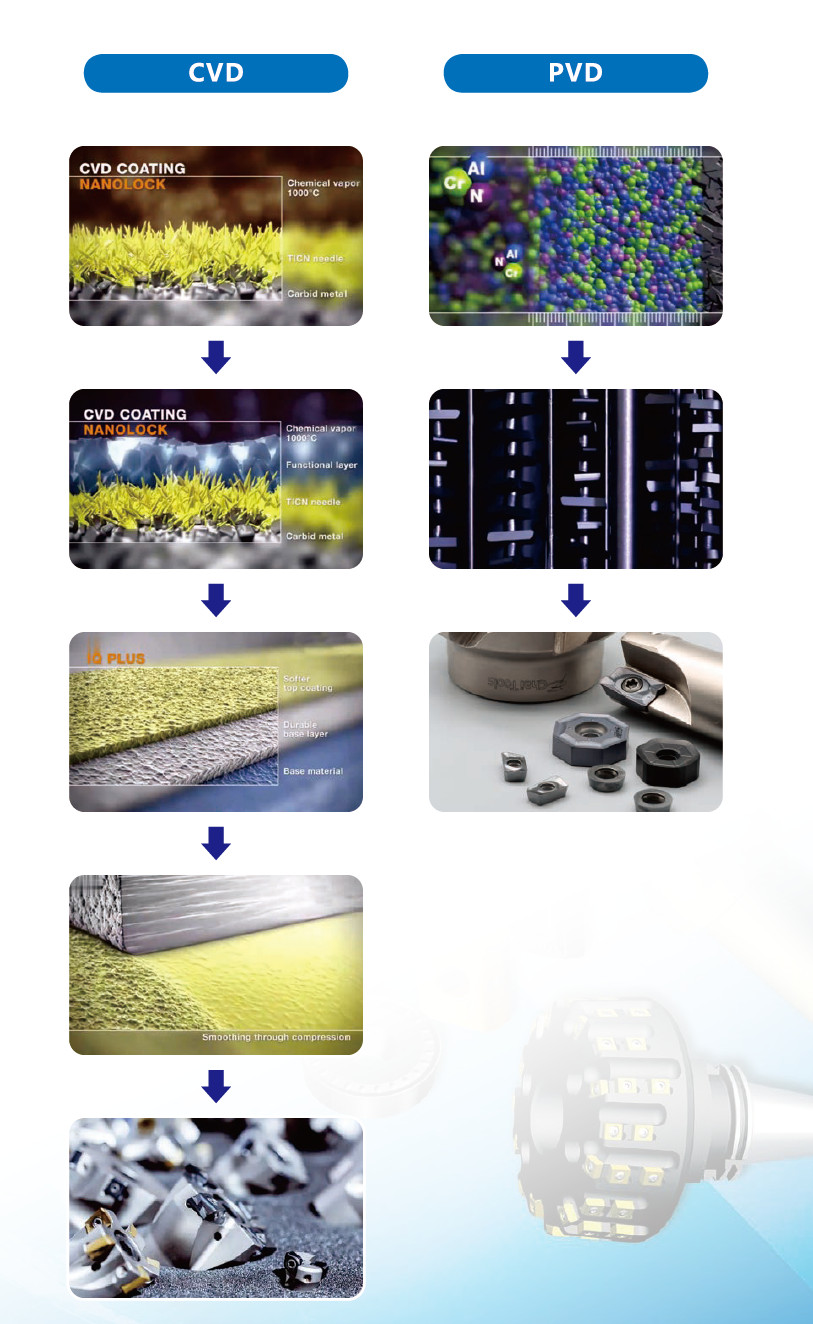
Certificates
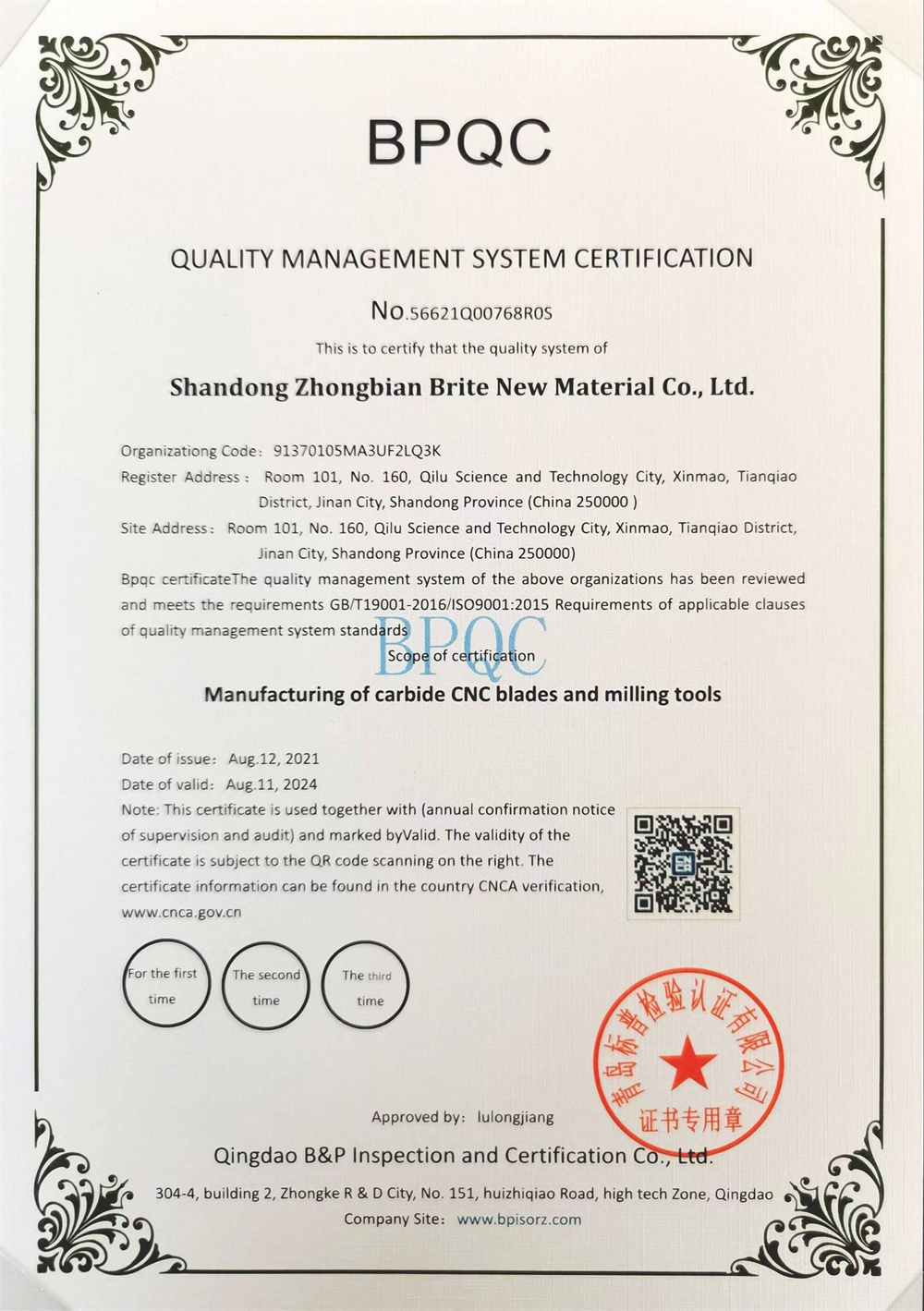
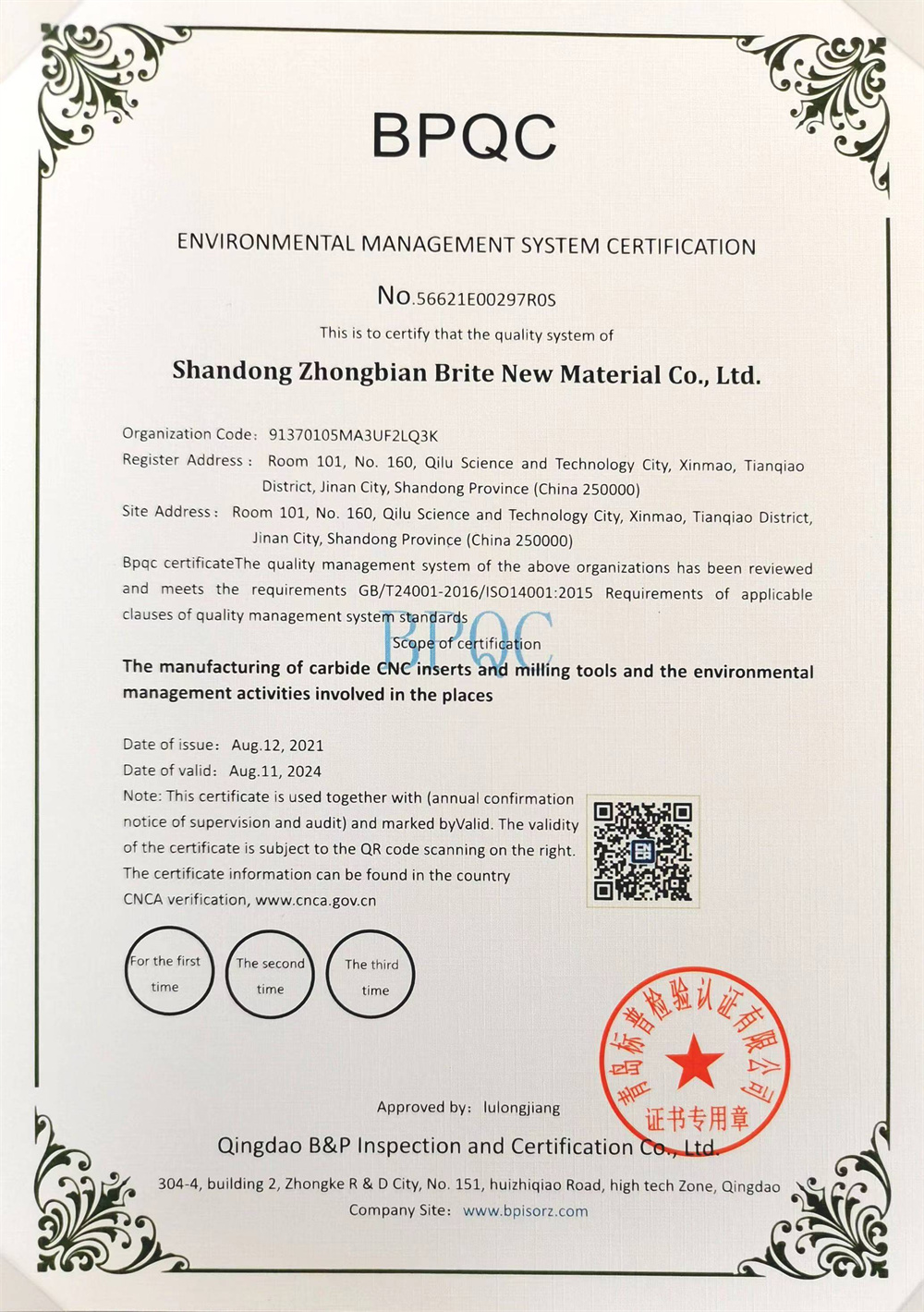
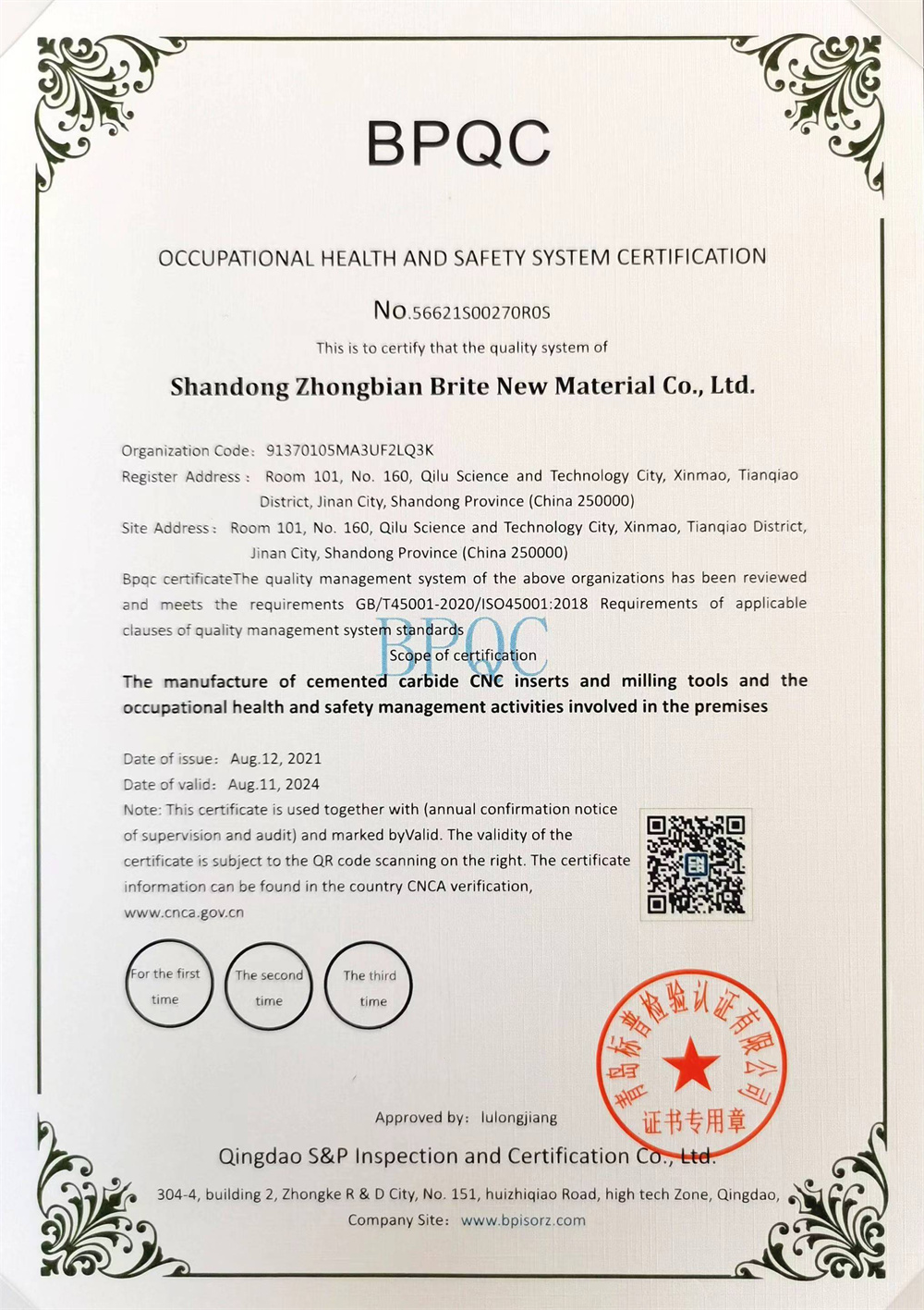
Production Equipment
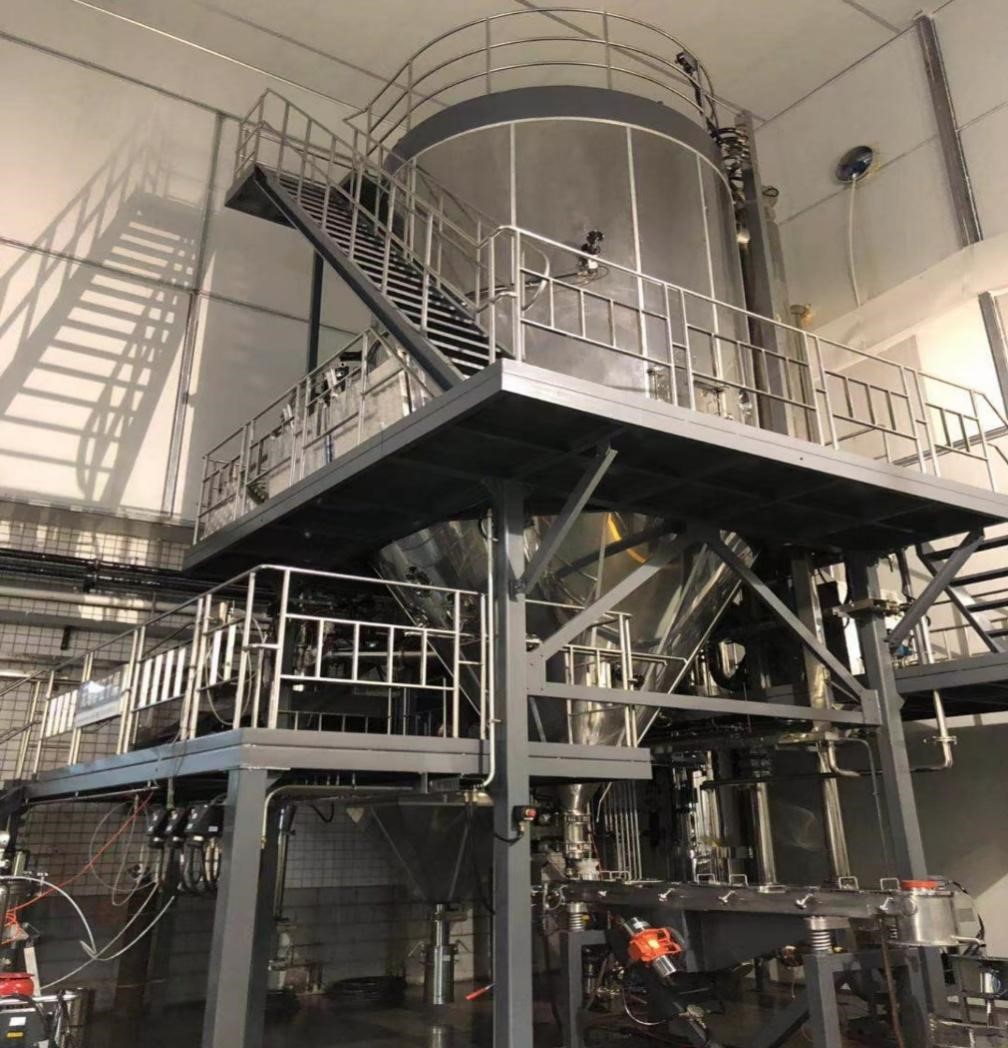
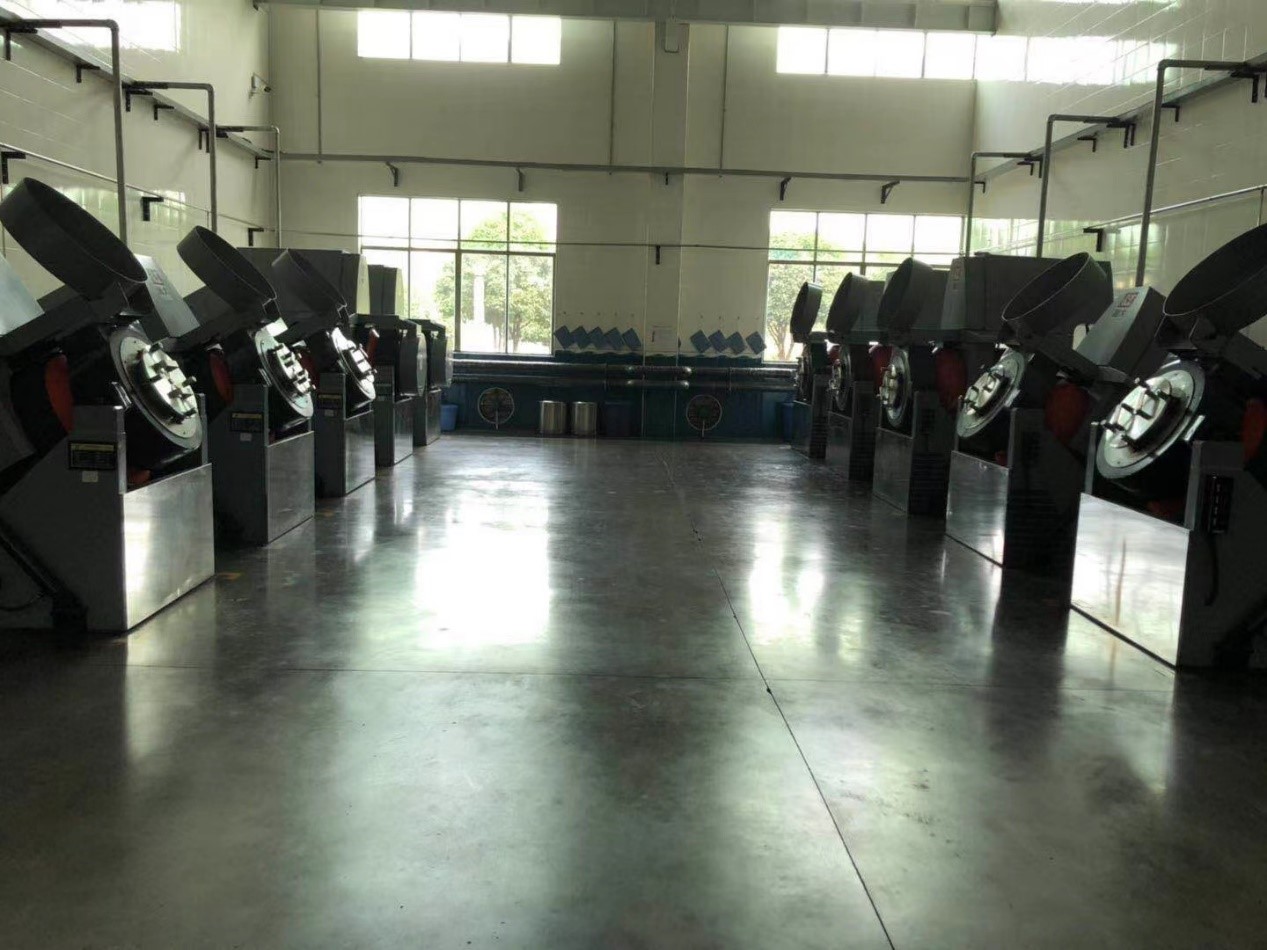
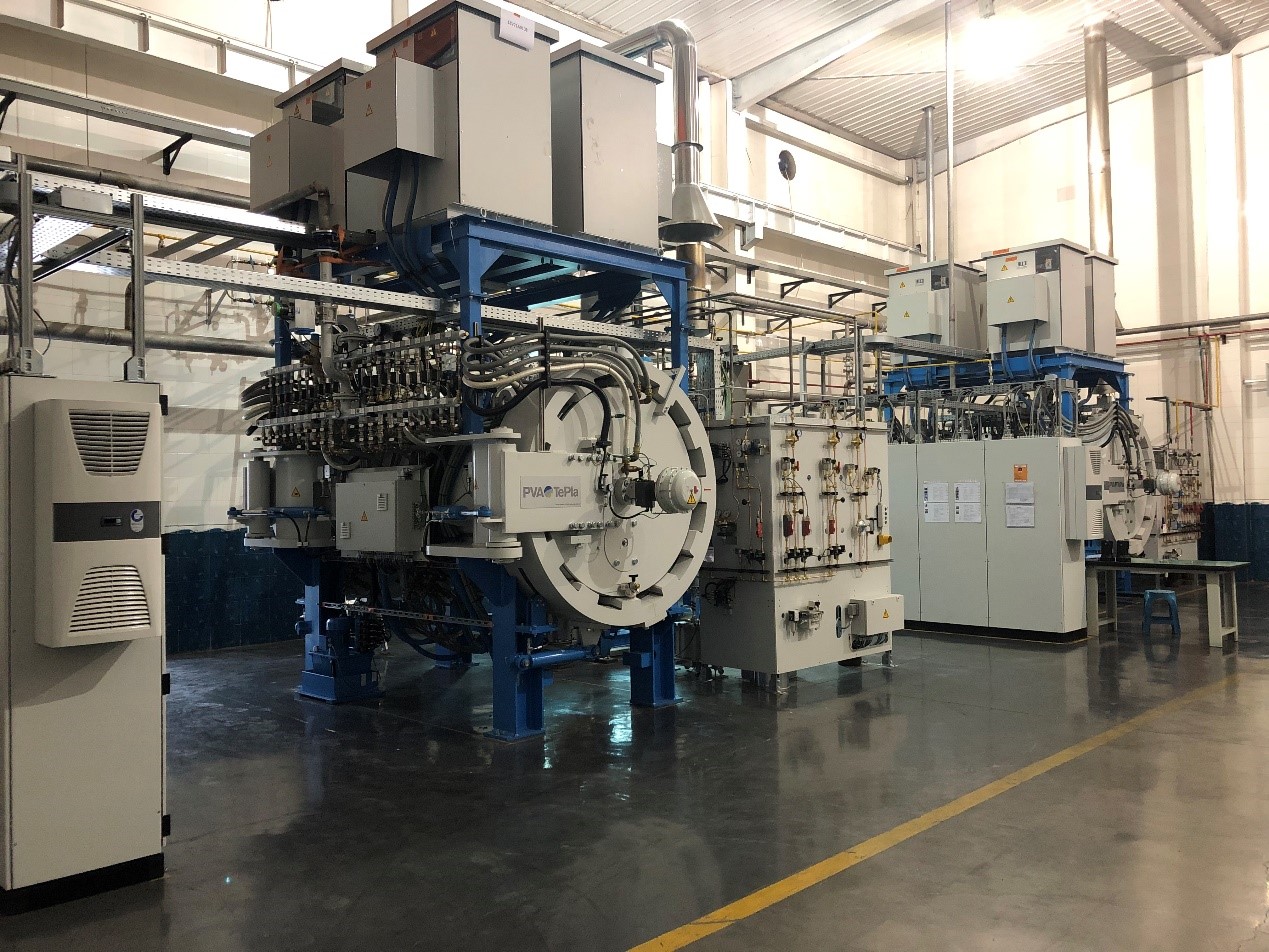
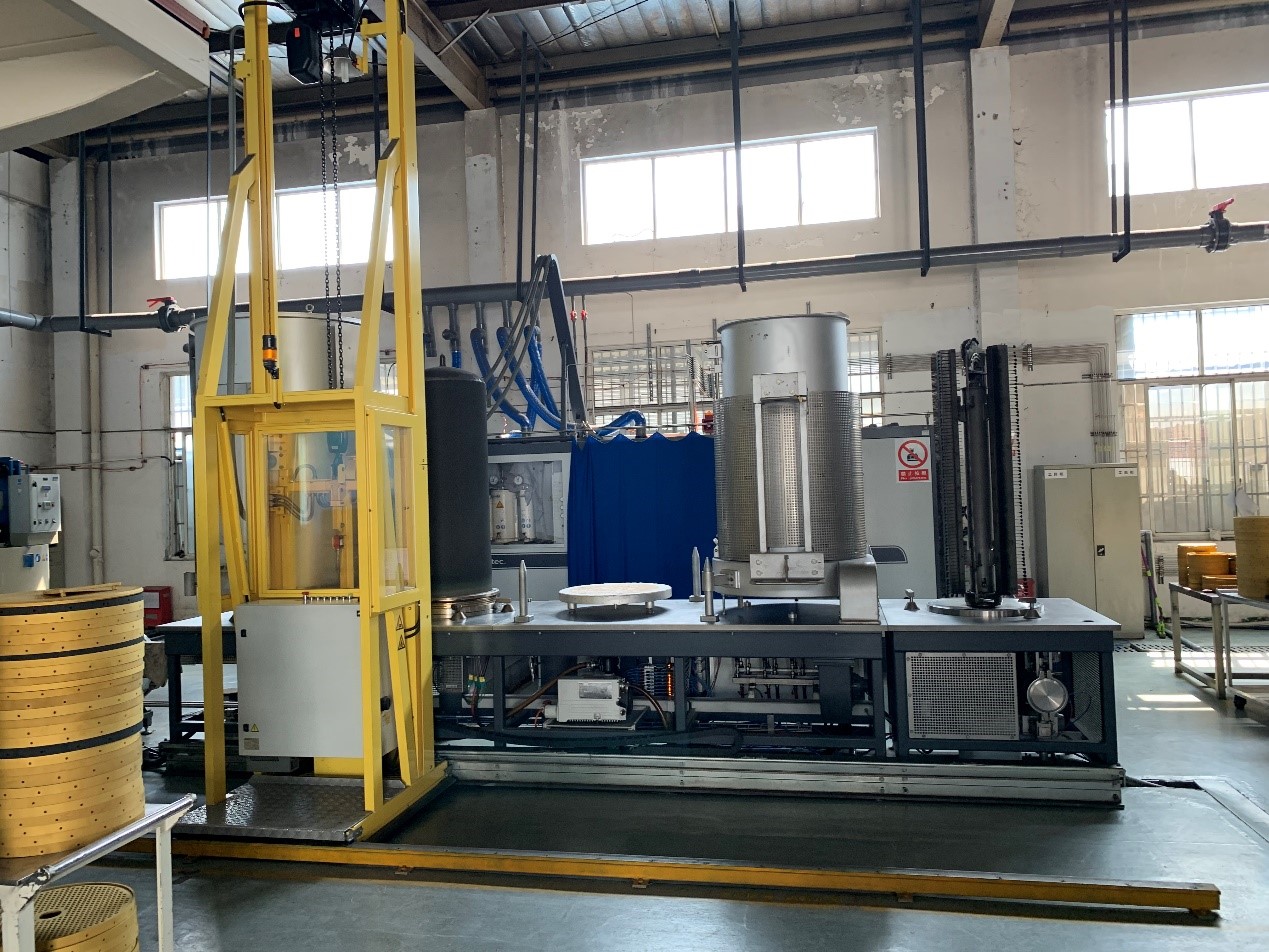
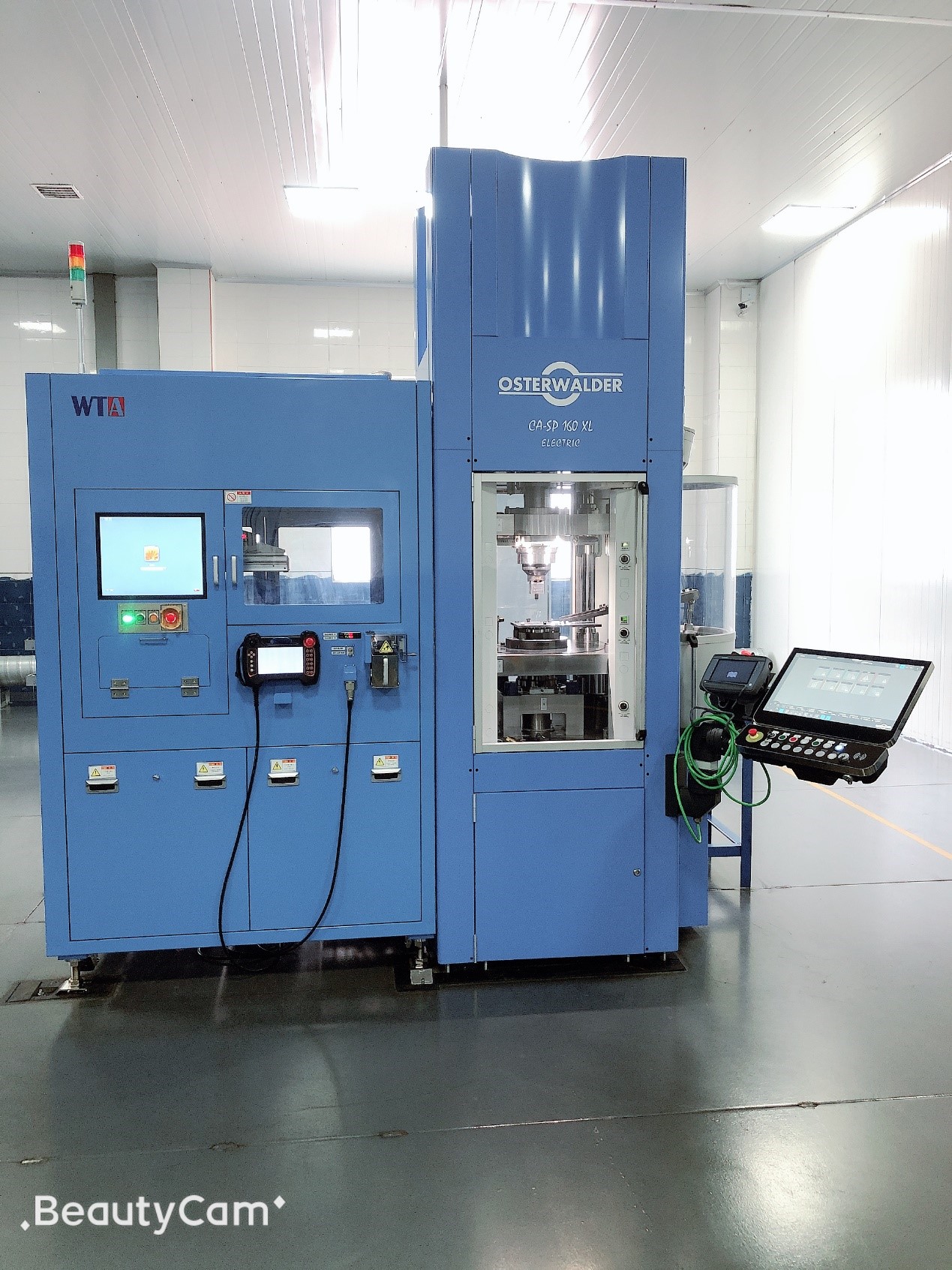
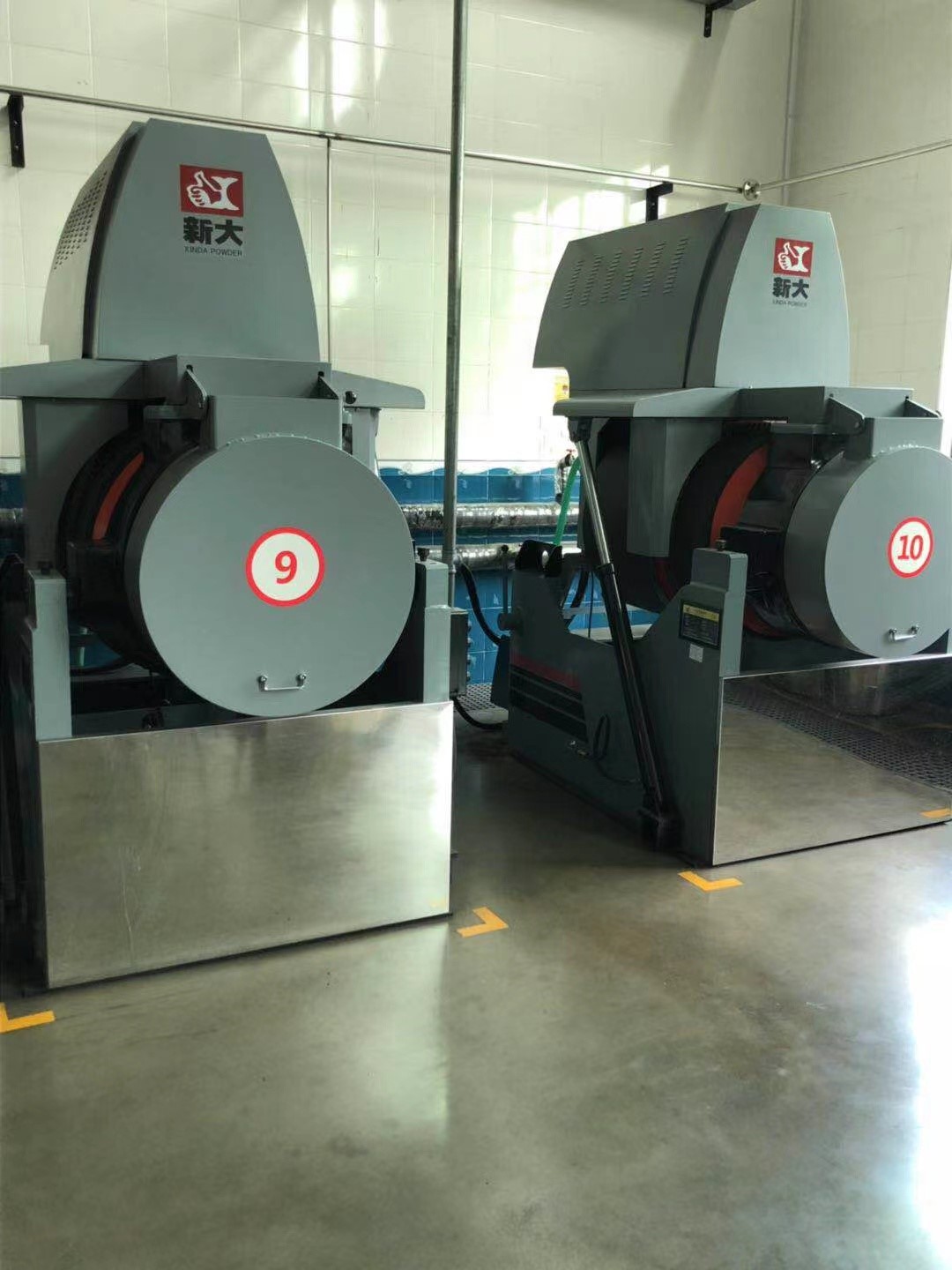
QC Equipments
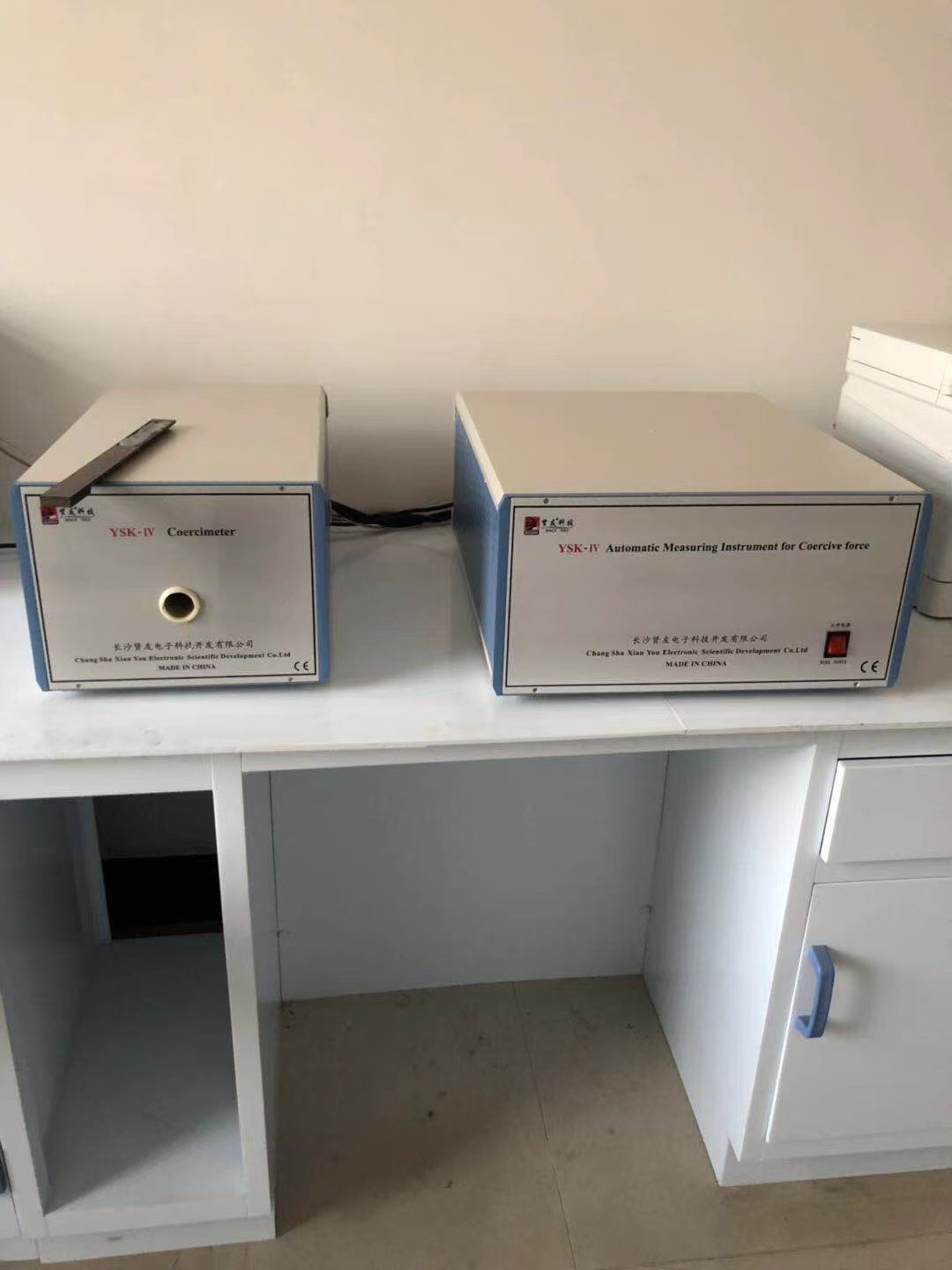
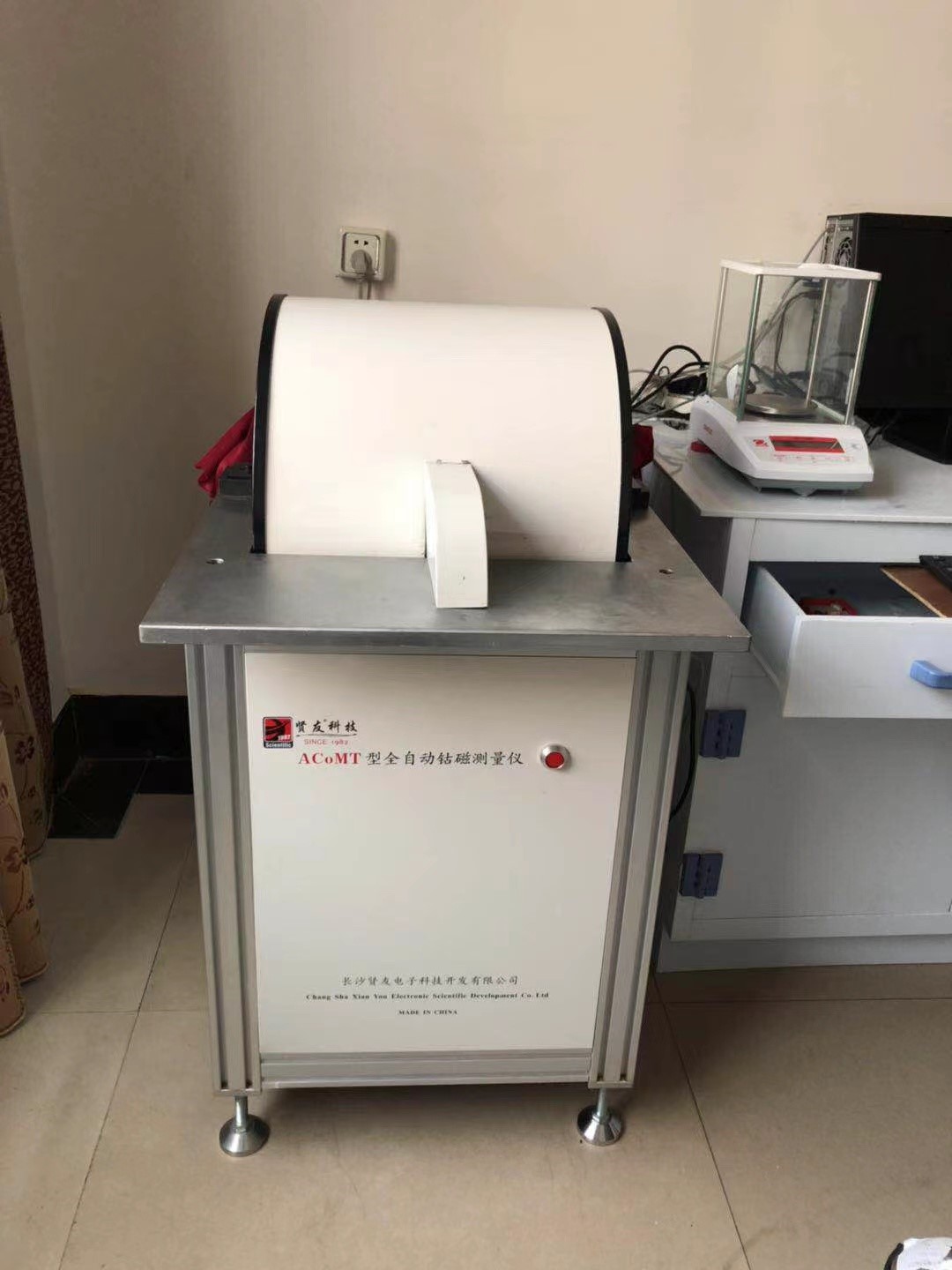
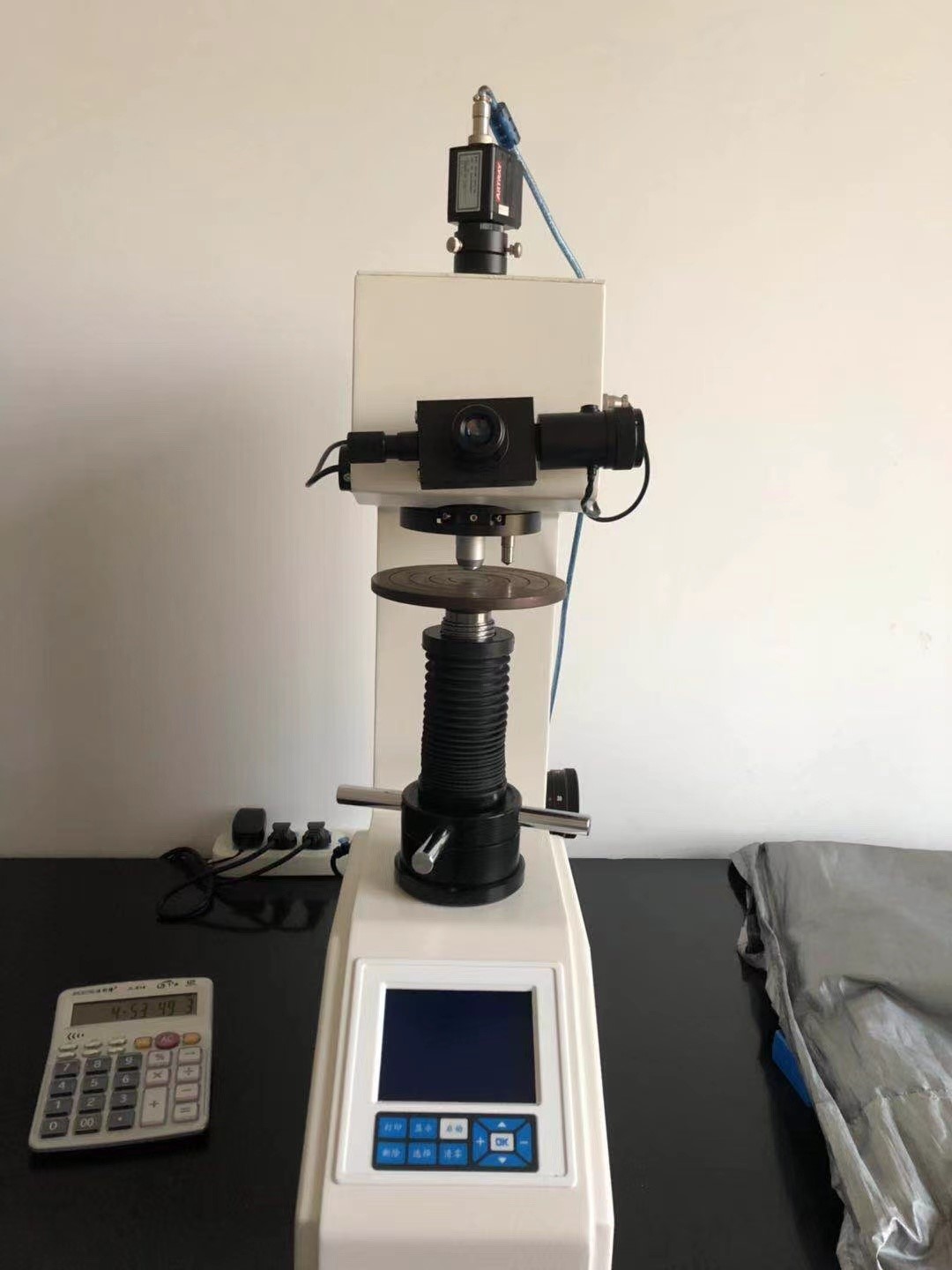
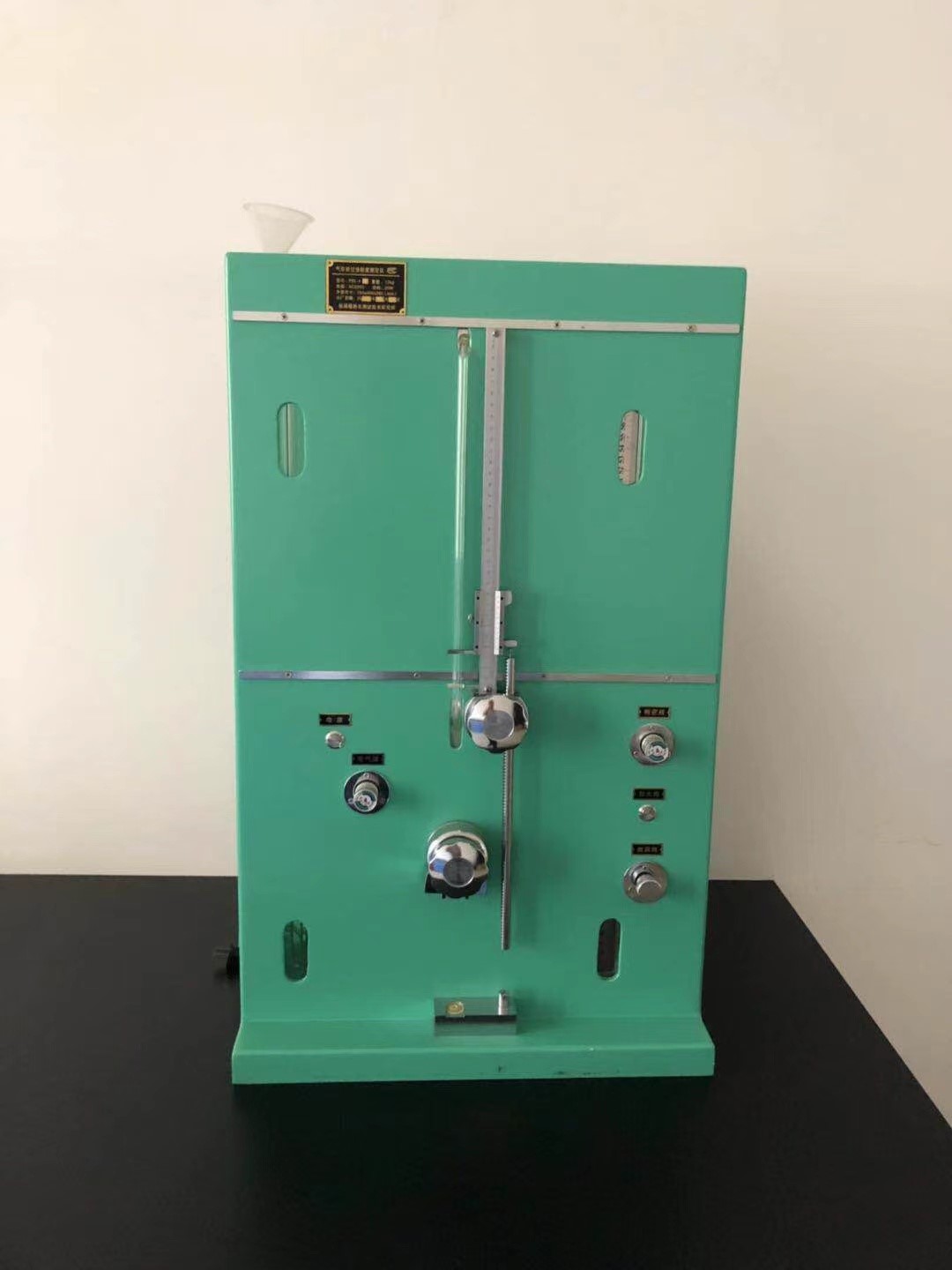
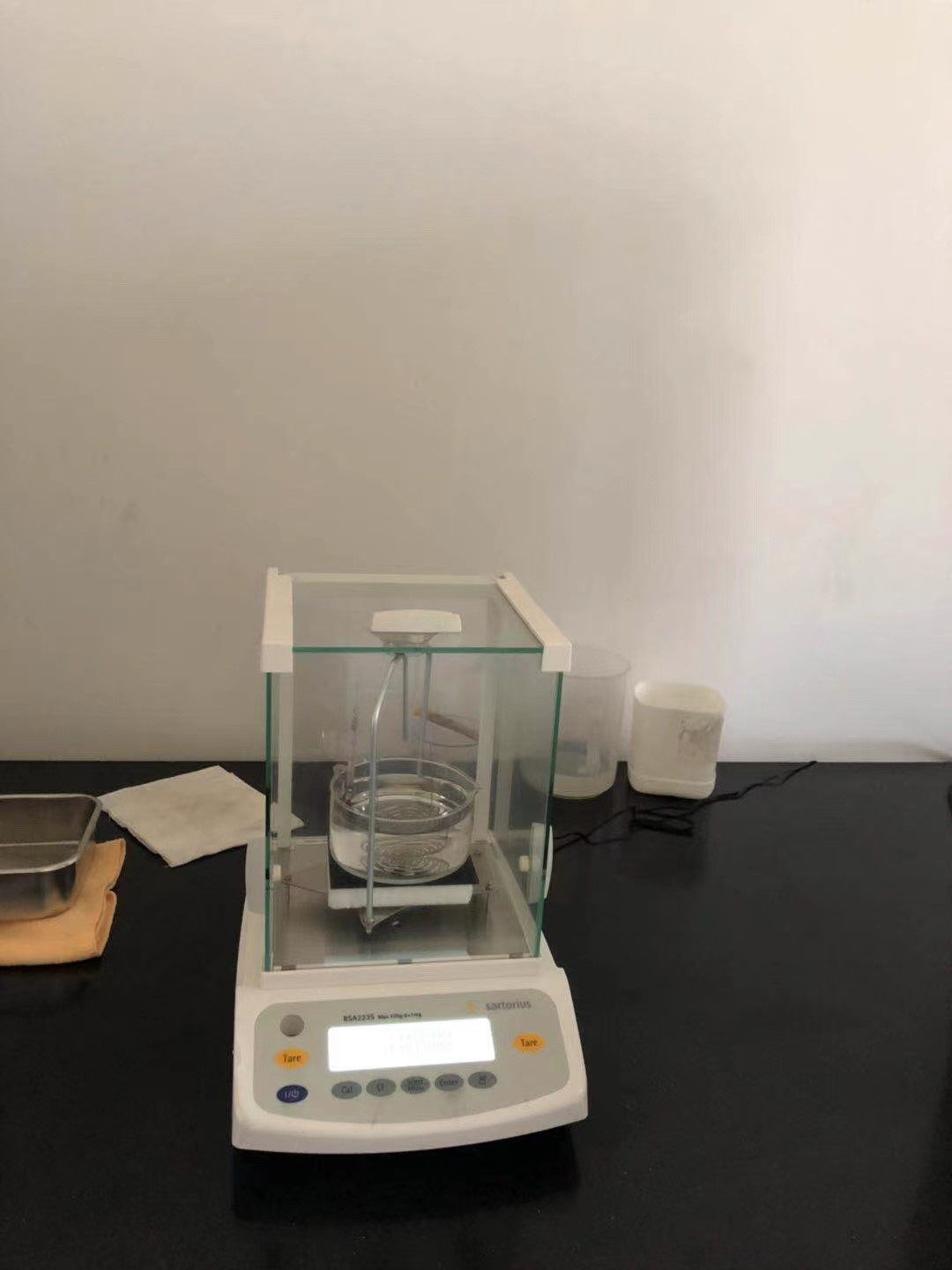
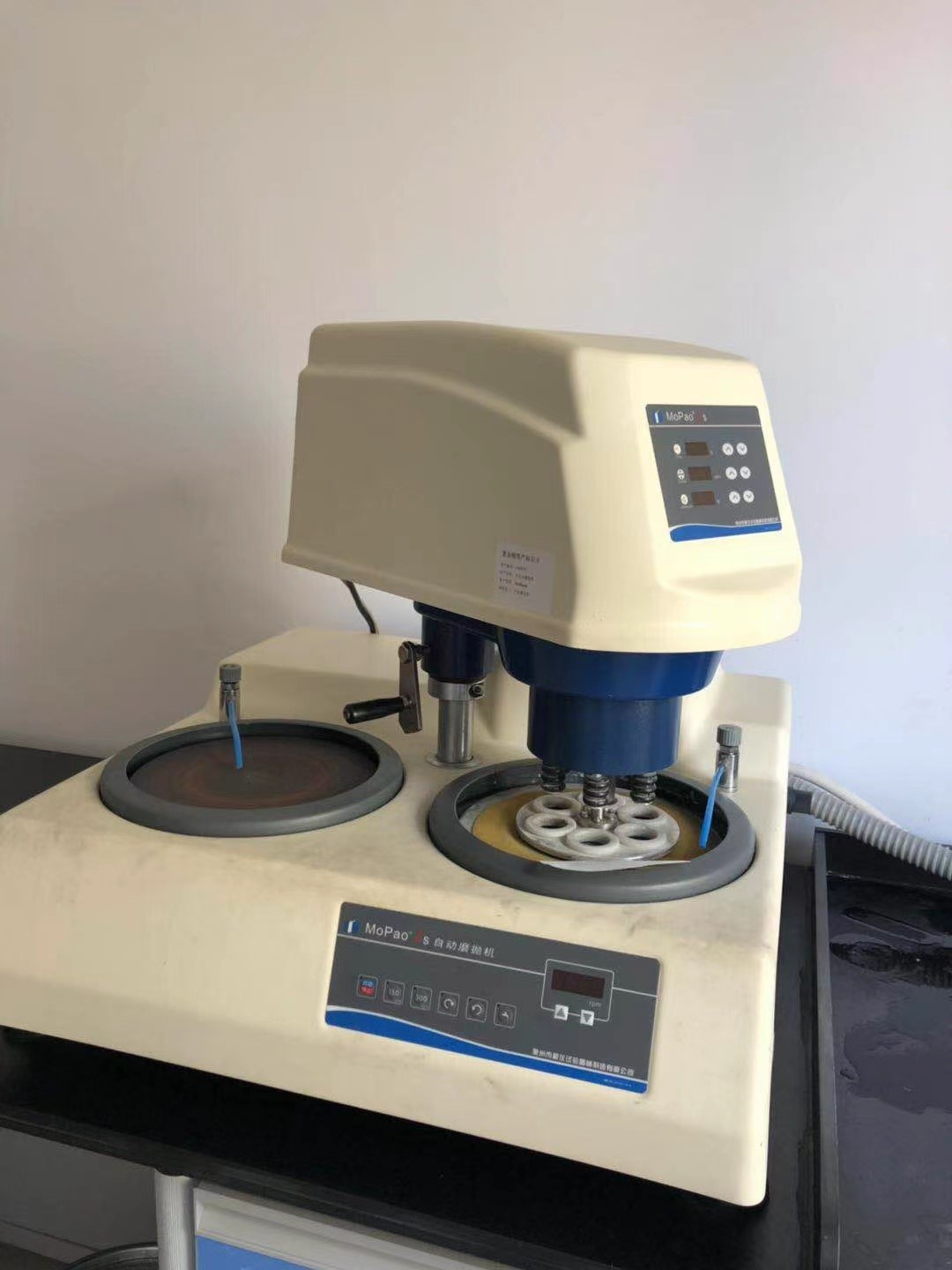
Advantages
1.Groove design,the cutting control is smooth, effectively reduce cutting resistance, to ensure longer tool life;
2.High quality materials;
3.Fine grinding process, we using imported production machine, automatic peripheral grinding process, higher precision, sharp wear
Our Services:
More than 2000 products are available. Assembly line production, high standard and strict requirements.
OEM Services Offered.
Customized Tools Offered.
Free laser marking on tools and boxes Offered.
Fast delivery time and Convenient Transportations. We have discount on shipping cost from our courier companies, such as FedEx, DHL, TNT, UPS etc.